Is It Time For An Installed Base Evaluation?
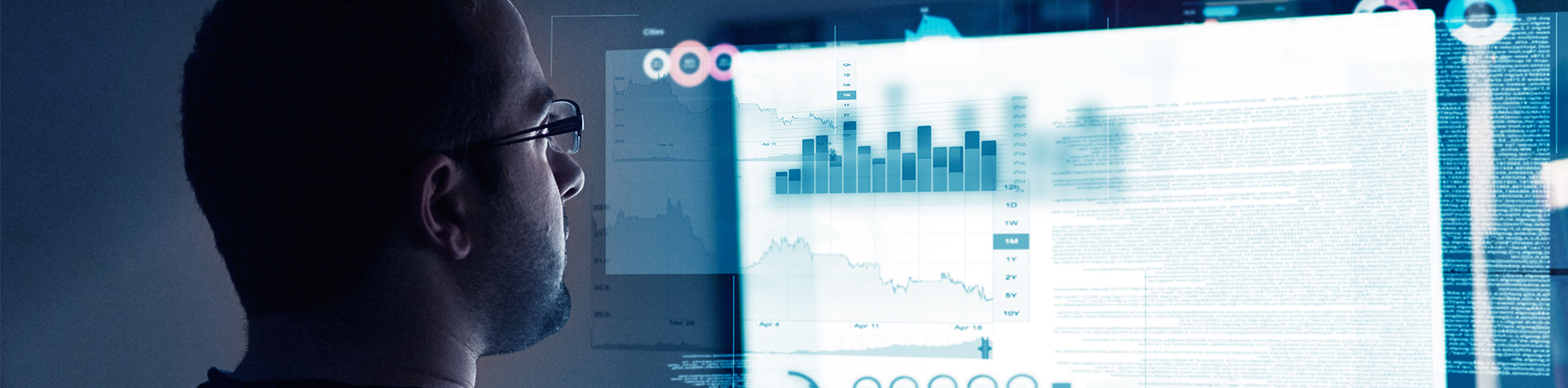
Installed Base Evaluations Help Organizations Better Manage Assets, Cut Costs and Reduce Risk
The majority of production facilities operating today are a mix of incredibly modern technologies and equipment operating well past its expected life cycle. Many companies are not entirely sure what equipment they have, or the specific risks that are associated with aging equipment. This is particularly important as manufacturers converge information technology (IT) and operations technology (OT) systems, and migrate to a unified Connected Enterprise.
The Installed Base Evaluation service can include a multisite Software Inventory Evaluation service or Installed Base Evaluation service, which is used to analyze critical plant assets to provide a full accounting and analysis of an organization’s IT and OT assets across the enterprise.
Organizations can use the Enterprise Installed Base Evaluation service to support specific corporate-wide initiatives, such as identifying their most critical assets, reducing obsolescence risks, managing corporate storeroom and spare parts initiatives, and ensuring all assets have up-to-date bills of material. For example, an organization can use the service to review its facilities for parts that are running business-critical activities, have no spare parts in inventory, and are also discontinued. This can help create a corporate risk profile that highlights the highest risk for downtime at each site.
Organizations attempting to do comprehensive evaluations in-house often spend a year or longer just to collect hardware data from a single facility straining high-value resources, especially when expanded across multiple facilities. It also presents challenges in ensuring a standard methodology is used for collection. With the Enterprise Installed Base Evaluation service, data can be collected and generate actionable, insights-based reports in mere weeks.”
Enterprise Installed Base Evaluation reports can provide insights across all of an organization’s facilities. They also can be customized based on top at-risk locations and top at-risk machines, or focus on specific business units across multiple facilities.
SMC is Rockwell Automation Certified for Installed Base Evaluation services designed to help manufacturers and industrial operators better manage their assets, cut costs and reduce risk, particularly as they converge IT and OT systems across plants and migrate to a unified Connected Enterprise.