Dairy Maximizes Production with Integrated Processing Plant
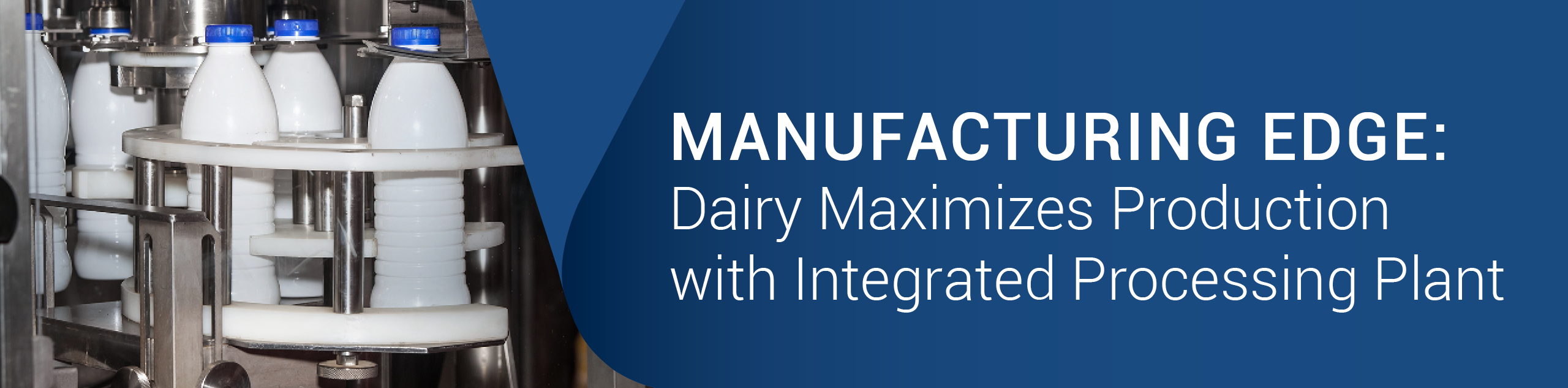
Challenge
The goal of the expansion was process optimization, manpower reduction (doing more through automation) and faster time to market. The dairy also focused on maintaining low operating margins. In addition, the control systems of various plants would need to integrate with the systems in the dairy. The plant required greater visibility and productivity, while optimizing resources including water, air, gas, electric and steam.
Solution
The goals of the plant included reducing batch cycle time to increase productivity of plant, and creating a flexible storage matrix for raw materials to improve operations. Given the scope and complexity of the project, the dairy recognized they needed a single vendor to manage the design and implementation of the control system. Choosing a company with the right set of skills and experience was critical. The dairy selected Rockwell Automation due to its extensive experience in automation and global reach.
Effective solutions included seamless integration on a single EtherNet/IP network; process optimization by deploying controller-based modular predictive control (MPC) on the pasteurizer; real-time energy monitoring; scalable engineering practices and standardization.
Rockwell Automation Global Solutions implemented a batch solution that:
- Monitors and controls 50 LLPD of milk daily.
- Allows operators to create and run different recipes, specify daily production rates and run multiple batches in parallel via the batch production entry system.
- Provides trending, alarming, and exception handling, as well as real-time monitoring of parameters at the refrigeration plant for energy saving.
- Allows the plant manager to have complete and accurate production information at any given time, and provided different types of reports, including performance, quality and material.
Results
The project was delivered by the Rockwell Automation Solutions Business through various OEMs. Each of these OEMs relied on Rockwell Automation control systems to enable plant-wide visibility and real-time monitoring. The dairy is now in discussions to create real-time dashboards for production and utility data. The solution increased productivity from five to 5.5 million liters per day. The dairy now enjoys a significant energy savings as clean-in-place (CIP) cycles have been reduced and temperature control is more precise and also, faster. Overall, the solution offers equipment OEE monitoring and real-time, role-based dashboard reporting tools for better decision-making.
Are you ready to see some results? Let the automation professionals at SMC help you meet your production goals with a Smart Manufacturing Solution.
The results mentioned above are specific to this dairy’s use of Rockwell Automation products and services in conjunction with other products. Specific results may vary for other customers.
Article Source: Rockwell Automation