Manage Downtime...Before its Too Late
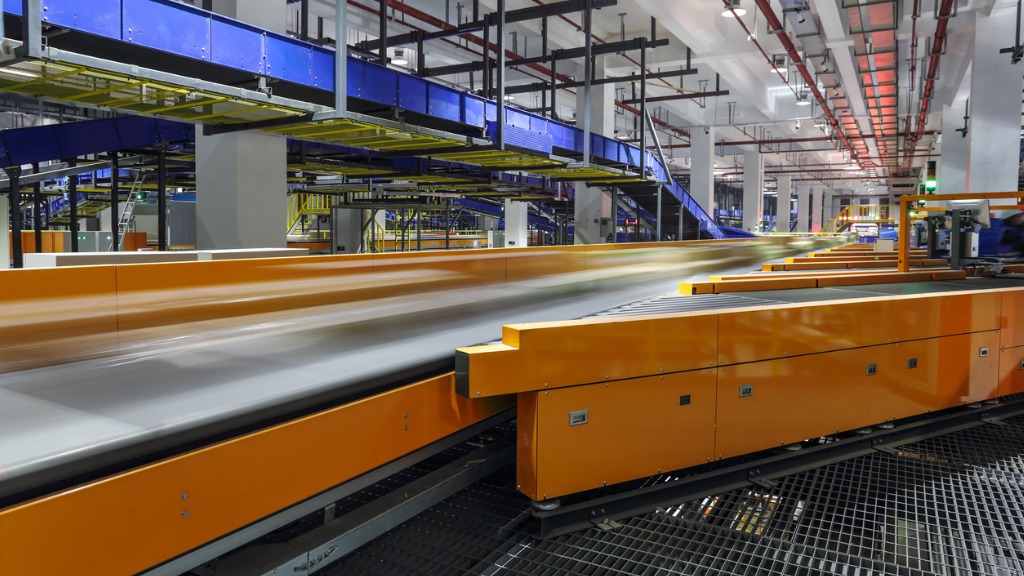
If there is one word that fills the owner or manager of a manufacturing plant with fear it’s probably “downtime.”
Downtime throws the entire schedule out of whack. It disrupts workflow, throws schedules into chaos and, worst of all, costs money. What are the causes of downtime in manufacturing, and what are some effective downtime reduction strategies to employ?
How to Manage Downtime
The primary cause of downtime in manufacturing is machine failure. If a particular machine is critical to your continuous production, then when that machine is not working, your factory is not working. There are many ways you can avoid or significantly reduce the circumstance of being in this scenario — here are five of them.
1. Set up a Regular Maintenance Schedule
Making sure you have a regular maintenance schedule for all your machines — and ensuring that plan is followed — is one of the easiest ways to reduce downtime. All machines wear down eventually, and making sure regular maintenance is performed on each one can extend the life of your machine’s parts and let you know when a part needs to be replaced. This way, you can do it before the machine shuts down and costs you valuable time. If you don’t have time or enough personnel to do this proactively, SMC offers preventative maintenance solutions that can remotely monitor your machine.
2. Ensure you have critical spares
It’s not always feasible or cost-effective for you to have a backup for every single machine in your manufacturing plant, but you should have replacement parts on your shelf to quickly replace the most critical parts within your plant. If you don’t know where to start, ask about an Installed Base Evaluation that will analyze part lifecycle as well as identify gaps of storeroom inventory compared to your installed equipment.
3. Remanufacturer Components back to OEM Specification rather than Repair them
Make sure you know who to turn to if one or more of your machines need an immediate repair. If your machine has to go out, you want to know it is going to work properly like if you bought a brand new item and also a repair provider that stands behind their work with extended warranties. If you’re not confident you’re going to get your machine back fully-repaired right away, you’re not working with the right repair company.
4. Properly Train Employees
Another reason machines break down more quickly than they should is that employees don’t always know how to use them correctly. You may not even notice how they cut corners or misuse a machine until it breaks down. You should be sure to train your employees not only in the proper use of their equipment, but also in any quick and effective fixes they can use when they encounter a problem rather than just shutting everything down.
5. Analyze and Plan Remediation
Take care to review unplanned downtime events and develop a maintenance plan that will reduce the downtime. If during your review you identify key areas for upgrade work with a company that takes the time to understand your process and can deliver on your expected outcome. These upgrades take time, work with your management to submit for capital upgrades or a local provider that can provide upgrades that will be implemented on a smaller scale.
Article Source: Klista Jardin, SMC Asset Manager