20 Benefits of a CMMS
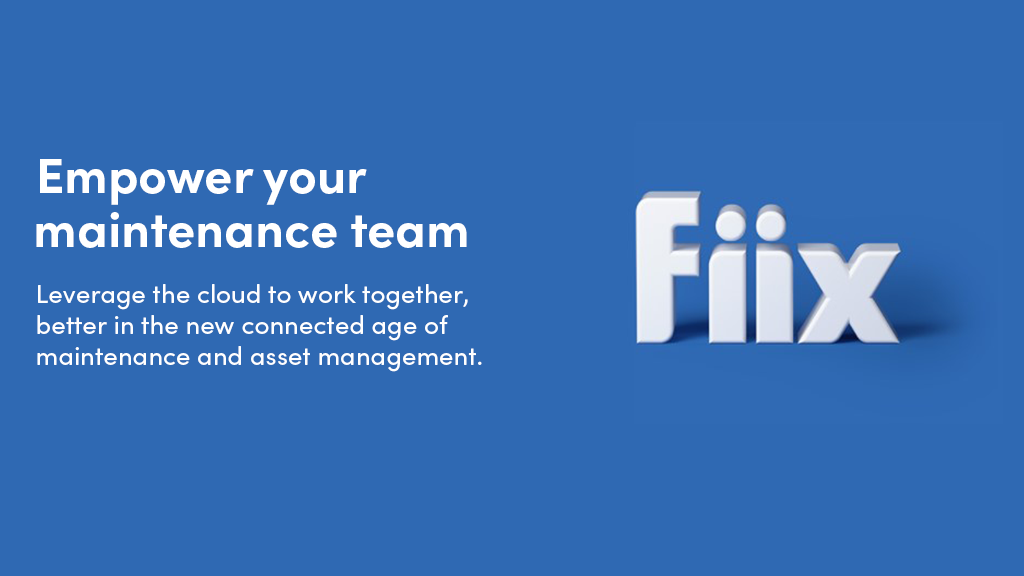
Why should you buy a CMMS? We know what introducing a new software solution at work isn’t easy— you have to spend time researching vendors, going through the sales process, justifying the cost, and training your team.
But the benefits of CMMS software are definitely worth the work, and can help you save time and money, improve health and safety, and more.
Reduce Downtime
1. Conquer maintenance backlog
Some degree of maintenance backlog is unavoidable, but too much can send your operation into a tailspin. Exhibit A: The cost of backlogged maintenance at US national parks is estimated to be $12 billion. This is an extreme case, but it illustrates the importance of keeping maintenance backlog at an acceptable level.
A CMMS balances resources and maintenance costs so backlog doesn’t get out of hand. The software captures small fixes that would otherwise go unnoticed and allows maintenance tasks to be scheduled, assigned, and prioritized so no jobs fall through the cracks.
2. Increase asset lifespans
The average age of industrial equipment in the US is the highest since the 1940's. Although age isn’t always the reason for failure, it’s often a contributing factor. It’s not always financially possible to replace old models with new ones, which is why maintenance is so crucial.
Keeping equipment in good operating condition for longer means doing maintenance before something breaks. You can’t do that using OEM guidelines or guesswork. Integrating CMMS software with sensors, PLCs, SCADA, and MES systems allows you to track an asset’s health in real-time, catch failure before it happens, diagnose problems, and schedule maintenance.
3. Make preventive maintenance easier to schedule and complete
Preventive maintenance catches defects before they become a bigger problem, which reduces the number of breakdowns. Maintenance teams know preventive maintenance is key to limiting downtime, but the question is, how do you schedule more of it?
A CMMS answers this question with automated work orders. PM triggers can be created based on usage, time, or condition in a CMMS. These triggers activate a work order, which is then scheduled and assigned. The work order becomes much smoother and preventive maintenance is easier to schedule, leading to less downtime.
4. Speed up repairs and inspections
Downtime occurs whenever an asset needs to be repaired or inspected. This isn’t always avoidable. However, if repairs and PMs are inefficient, it prolongs downtime. These inefficiencies can add up and cost your facility a lot of time and money in lost production.
A CMMS makes it easier to repair and inspect assets so downtime is reduced to the bare minimum. Technicians can log into a mobile CMMS app from anywhere and see an asset’s history, diagrams, the location of spare parts, and more so work can get done faster. CMMS software can also help you find work orders that take too long, spot the cause of the delay, and fix it so work can get done faster.
Control Costs
5. Accurately forecast the parts you’ll need for maintenance
Not having a handle on inventory can lead to all sorts of costly problems. Overspending on inventory can add an additional 12% to 20% to the original purchase cost. If you don’t have the right parts on-hand when equipment breaks down (or can’t find the parts in a messy storeroom), it results in downtime, rush shipping, and risky stopgap measures, all of which are expensive.
Managing your inventory with a CMMS helps you purchase, track, and organize parts so you can avoid these costly problems. Tools, like automated purchasing, inventory reporting, and AI-powered parts forecasting can help you make data-driven inventory decisions and eliminate over and understocking.
6. Avoid manufacturing scrap and rework
Both scrap and rework require a huge cost in the form of energy, waste, and lost production. The worst part is, it’s extremely difficult to make up for that expense without the production team working overtime.
The best way to reduce the cost of scrap and rework is to avoid unplanned failure by keeping assets healthy with preventive maintenance. CMMS software excels at helping maintenance teams plan, schedule, and execute PMs. Not only can you automate tasks with a CMMS, but you can also prioritize and assign PMs while tracking key metrics to optimize them.
7. Track and report on maintenance costs
CMMS software tracks everything connected to completed work orders, including parts, labor and other expenses. This makes it easy to run a report on these costs, view where the budget was spent, and make educated capital expenditure decisions. If you’re looking to prove the value of maintenance, you can even compare the cost of reactive and planned maintenance.
8. Save energy
American manufacturers spend $230 billion on energy every year, which just goes to show that any company can cut costs by reducing energy use. Well-maintained assets are more energy-efficient and are key to lowering your overall energy expenses.
Reactive maintenance is a major source of wasted energy at production facilities because it leads to inventory issues, poor scheduling, rework, and more. A CMMS can solve each one of these issues by helping you establish a better preventative maintenance program with tools like automated work orders and easier work scheduling.
Increase Efficiency
9. Optimize your maintenance schedule
Well-planned maintenance schedules waste less time, resources, and money. Better planning is possible when you can anticipate every element of maintenance, like asset needs, production schedules, and inventory.
Building a better maintenance schedule starts with understanding your assets and resources. Tools like sensors, PLCs or MES systems help you capture, track, and analyze data about an asset’s performance. Integrating these tools with CMMS software allows you to use this data to fine-tune the frequency of preventive maintenance tasks and ensure maintenance schedules use staff resources as effectively as possible.
10. Automate work requests
It’s common for maintenance managers to receive work requests via phone, sticky notes, whiteboard, or word of mouth. None of those are ideal. These outdated processes force maintenance teams to spend unnecessary time creating work orders and inputting data.
CMMS software eliminates all the extra steps by automating the work request process. Employees can log work requests, set up PM triggers, or connect to sensors that create work orders based on the real-time condition of an asset. No time is wasted translating work orders, tracking down operators, or rifling through a file cabinet.
11. Standardize maintenance processes
One tried and true way to make maintenance more efficient is to use a tool you know works well in a certain situation. Starting from scratch with every PM, repair, or report will take longer and lead to extra downtime and costs.
A CMMS gives you the power to build maintenance checklists, workflows, reporting templates, and more to make tasks easier and quicker. It also makes these resources available digitally, so everyone can access the same information, follow the same best practices, and get the job done as quickly as possible.
12. Improve access to maintenance resources
A lack of centralized knowledge means having to track someone down, shuffling through stacks of paper, or searching through a computer to find the solution to a breakdown. These little inefficiencies lead to bigger problems, like more downtime and failed audits.
A CMMS makes maintenance resources readily available to anyone, at any time by providing a centralized hub for information. Attach videos, manuals, task lists, accident reports, inventory requirements, and more to any piece of equipment or work order to help technicians get tasks done in less time.
13. Find trends in maintenance metrics
Maintenance metrics translate action into numbers so you can measure the performance of everyone and everything in your operation. They allow you to connect cause and effect so you can make better decisions and improve your operation.
You can’t track metrics without the right tools, processes, and people. CMMS software is the ‘tools’ part of this equation. It captures the numbers and tracks metrics over time so you can get a long-term view of your performance. It also makes it easier to analyze the metrics and fine-tuning strategies based on the data.
14. Save time on reporting
Maintenance KPIs help you identify chronic equipment problems and benchmark against industry standards. However, compiling KPI reports using Excel or pen and paper can be tedious and lead to mistakes.
CMMS software allows you to collect data from various areas of your maintenance operation and make sense of them with reporting templates. A CMMS can often automatically send reports to your inbox on a set schedule. Having a better understanding of your KPIs helps you add value or reduce risk with small changes. Quickly analyze trends, spot recurring problems, track costs, and more.
15. Collect real-time work order updates
Being able to track the progress of work orders is crucial for limiting backlog, creating effective schedules, planning production, and building budgets. If the right people don’t have visibility into work orders, it leads to more downtime, higher costs, and uninformed decision-making.
A CMMS helps you avoid these nightmare scenarios. The software provides real-time work order updates, like the priority status, who is assigned to it, and how long it’s taking, so you can allocate additional resources if needed. A CMMS also notifies production staff when assets are back online, so they can get back to work without delay. The system can even tell you which work orders are causing delays, downtime, or extra costs so you can figure out why and stop it.
16. Access historical information
It’s difficult to manage an asset through its entire lifecycle if you don’t know its history. Even if your technicians know everything about an asset’s past, high turnover and retirement rates mean this information is never far from being lost forever.
A CMMS provides a defense against this sort of brain-drain. Each asset has its own unique record that details everything that’s been done to it, from repairs to inspections, labor hours, and more. Technicians can quickly access these records to assist with PMs or troubleshooting a failure.
Improve Health and Safety
17. Reduce risk on every job
It doesn’t matter if a job is done quickly if it isn’t done safely. The chances of an accident increase when safety isn’t part of the planning process. Ensuring every job is safe adds a few extra steps when creating a work order, but it’s well worth it to keep your team healthy.
A CMMS makes it easier to create work orders that have the well-being of the maintenance team in mind. You can add checklists, material safety data sheets, safety procedures, and required PPE so you can be sure technicians are doing a job safely and avoiding risks.
18. Prepare for audits in less time
Audits aren’t always easy to pass and it’s even more difficult without the right tools and know-how. And the prospect of failing an audit brings with it huge headaches and the risk of losing thousands or millions of dollars.
CMMS software makes it easier and more cost-effective to prepare for an audit. It helps facilitate inspection rounds and makes it possible to search the system for maintenance records of a certain asset or time period. Documenting compliance activities is also simpler with a CMMS as it gives you the chance to create reports and store photos.
19. Steer clear of OSHA violations and fines
Safety violations lead to more accidents and can take a toll on the bottom line, costing businesses millions of dollars in fines. These violations often happen when people are missing information, expectations aren’t clear, and communication breaks down.
A CMMS can be the solution to these issues. Safety procedures can be made more accessible and visible on checklists and asset profiles. Technicians can pull up these procedures on their phones within seconds so they never miss important safety instructions that could lead to a violation.
20. Manage safety training
Training is a key element of safety— it’s been shown to reduce injuries by 24%. It also leads to fewer breakdowns and unforeseen costs. Although safety training is crucial, everything from bad timing to the need for specialized skills can hinder your team’s best-laid plans.
CMMS software can help remove the obstacles in the way of proper safety training. A CMMS allows you to store and track health and safety information for technicians, like certifications. You can also pull safety reports from the CMMS so you can decide what kind of training should be prioritized.
BONUS BENEFIT: Connect with maintenance experts
Working in maintenance can often feel like you’re on an island. That can be lonely, frustrating, and a roadblock for reaching personal and team goals. Connecting with other maintenance professionals is one way to overcome this challenge. It gives you the chance to ask questions, trade ideas, troubleshoot problems, and learn from people who have been in your position.
A CMMS doesn’t do any of this. But your CMMS vendor can if you choose the right one. A great CMMS provider gives you more than just software—it gives you access to a community of experts and maintainers to help you achieve world-class maintenance, whether that’s through conferences, events, social platforms, or training packages.
CMMS software is more than a one-trick pony
Every person in a facility has a different goal, from completing maintenance to tracking metrics or reducing costs. Regardless of what you’re trying to achieve, CMMS software makes it easier to accomplish. The real value of maintenance software lies not in its features, but in the way those tools are used to eliminate inefficiencies, identify areas of opportunity, and maximize the talent at your facility. A CMMS makes all of this possible, and more.
Article Source: Fiix Software