How a Maintenance Manager Modernized his Facility and Cut Reactive Maintenance by 54%
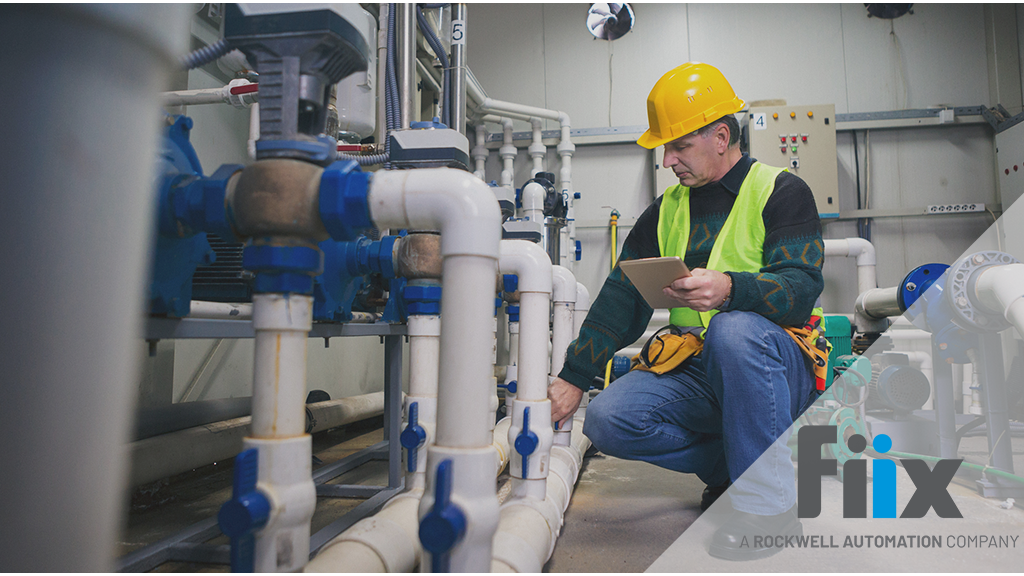
Tom has been hard at work modernizing the Perth County Ingredients (PCI) facility that he’s worked at since 2017, where he has implemented both a building automation system (BAS) and a computerized maintenance management system (CMMS). As anyone could imagine, implementing two plant-wide systems over a three-year span is no small feat.
The results speak for themselves, however. Tom’s work has directly contributed to a
Early Efforts at the Dried Egg Processing Facility
Tom’s work at PCI actually predates his current role. He joined the company’s dried egg processing facility as a contractor back in 2012. Having worked at the facility for five years when he took on his current role, he went into the job already having an intimate knowledge of the plant.
“When I started [full time], there was a large need for us to upgrade our facility. We needed new boilers, new chillers, that sort of thing,” says Tom.
What’s more, the maintenance team was wasting time and resources. 100% of the maintenance was reactive—meaning the team couldn’t move beyond trying to put out fires all day.
Tom knew his facility was in desperate need of a solution that could let them get ahead of maintenance and start planning it, rather than reacting to it. His team also had very little insight into after-hours emergency calls. The maintenance team would get alerted, and someone would have to respond, whether it was pressing a reset button or a repeat problem that could easily be solved.
Finding a Better Solution
The facility’s BAS system was already in place, but Tom knew more was needed to get things under control. He needed a solid CMMS software and made the choice to use Fiix. It didn’t take much to get started.It was quite simple. The minute you start adding assets, you start making work orders, you start making scheduled maintenance, your team stops relying on you for that day-to-day, ‘What would you like me to do today, Tom?’ Now you have that in the maintenance software.
Not only did implementing Fiix allow Tom to focus on managing the maintenance team, it also gave him the value-added time to project manage a $4M capex investment for the facility.
As it turned out, Fiix was exactly the puzzle piece Tom’s facility needed. He provided tablets with the Fiix app to the entire maintenance team, which support scanning, access to the BAS, access to all standard operating procedures (SOPs), and the ability to search old work orders to cut down on troubleshooting time.
Rolling Out Automation Company-Wide
Tom’s instincts paid off. The success at his facility was also noticed by the VP of operations, who asked Tom to start rolling the system out at more facilities. Before he knew it, Tom was hard at work implementing Fiix at seven other L.H. Gray facilities across the country.
The automation within our facility has basically allowed us to run multiple operations from one location. I get email alarms along with the production manager, so our fingers are always on the pulse of the facility. Without being there, you still know what's happening.
This proactive move has served PCI well in the age of COVID-19. “Putting in these measures for automation has allowed us to bring down the amount of people who need to be in one place at one time,” says Tom. What’s more, the control that Fiix grants him allows Tom to roll out the remaining implementations remotely, with no plans of slowing down anytime soon. “If you’re standing still, you’re falling behind,” says Tom. “We are constantly driving for more automation and growing.”
Article Source: Fiix Software